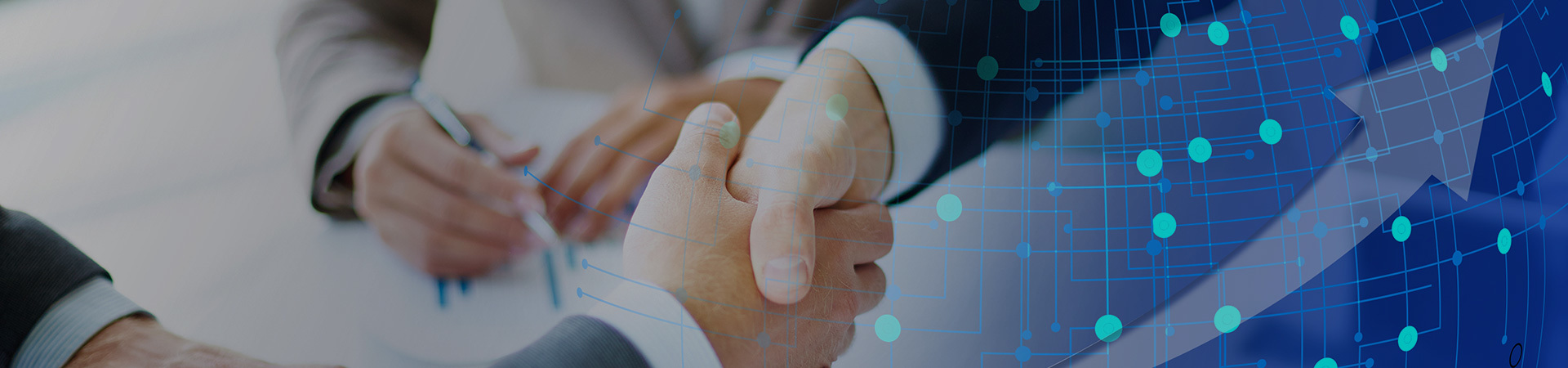
多くの人が型材ラジエータの成形過程に興味を持っていて、一体どのような加工がこのようにすることができて、とても精密で、今日私たちはあなたのために秘密を暴きます!
アルミニウムダイカスト技術
アルミニウム押出技術のほか、放熱フィンを製造するためによく用いられる別の製造方法はアルミニウムダイカストであり、アルミニウムインゴットを溶解して液状にした後、金属模型内に充填し、ダイカスト機を利用して直接ダイカスト成形し、放熱フィンを製造し、ダイカスト法を用いてフィンを多種の立体形状にすることができ、放熱フィンは需要に応じて複雑な形状にすることができ、ファンと気流方向に合わせて導流効果のある放熱フィンを製造することもでき、しかも薄くて密なフィンを作って放熱面積を増やすことができ、技術が簡単なため広く採用されている。一般的によく使われるダイカスト型アルミニウム合金はADC 12であり、ダイカスト成形性が良好であるため、薄い鋳物に適しているが、熱伝導率が比較的に悪い(約96 W/m.K)ため、現在国内ではAA 1070アルミニウム材料をダイカスト材料とすることが多く、その熱伝導率は200 W/m.K程度に達し、良好な放熱効果がある。
しかし、AA 1070アルミニウム合金でダイカストされたヒートシンクには、それ自体では克服できない先天的な不足がいくつか存在している:
(1)ダイカスト時に表面流紋及び酸化スラグが多すぎると、熱伝達効果が低下する。
(2)冷却時に内部微細孔が高くなり、実質熱伝導率が低下する(K<200 W/m.K)。
(3)金型は侵食されやすく、寿命が短い。
(4)成形性が悪く、薄い鋳物には適さない。
(5)材質が柔らかく、変型しやすい。
CPUの主周波数の継続的な向上に伴い、比較的に良い放熱効果を達成するために、ダイカスト技術を用いて生産されたアルミニウム質放熱器の体積は絶えず増大し、放熱器の設置に多くの問題をもたらし、しかもこの技術で製作された放熱フィンの有効放熱面積は限られており、より良い放熱効果を達成するためには必ずファンの風量を高め、ファンの風量を高めるとさらに大きな騒音が発生する。
アルミニウム押出技術
アルミニウム押出技術は簡単に言えば、アルミニウムインゴットを約520 ~ 540℃に高温加熱し、高圧下でアルミニウム液を溝を有する押出型金型に流し、フィン初胚を作製したが、さらにフィン初胚を裁断、溝切りなどの処理を行った後、私たちがよく見るフィンを作製した。アルミニウム押出技術は実現しやすく、設備コストが相対的に低く、前年のローエンド市場でも広く応用されている。一般的に使用されるアルミニウム押出成形材料はAA 6063であり、良好な熱伝導率(約160 ~ 180 W/m.K)と加工性を有する。しかし、自身の材質によって制限された放熱フィンの厚さと長さの比は1:18を超えることができないため、限られた空間内で放熱面積を高めることは難しいため、アルミニウム押出フィンの放熱効果は比較的に悪く、現在ますます上昇している高周波CPUに適任することは難しい。
フレキシブルプロセス
可撓性プロセスは、まず銅またはアルミニウムの薄板を成形機で一体成形されたフィンに折畳み、それから穿刺型で上下底板を固定し、さらに高周波金属溶着機を利用して、加工された台座と一体に溶接し、プロセスは連続接合であるため、高厚比のフィンに適しており、フィンは一体成形であるため、熱伝導の連続性に有利であり、フィンの厚さは0.1 mmしかなく、材料の需要を大幅に低減することができ、そして放熱フィン許容重量内で最大熱伝達面積を得た。大量生産を達成し、材質接合時のインターフェースインピーダンスを克服するために、製造工程部は上下底板を採取して同時に材料を送り、一貫製造工程を自動化し、上下底板接合は高周波溶接接合を採取し、すなわち材料の融着はインターフェースインピーダンスの発生を防止し、高強度、密列間隔の放熱フィンを構築する。製造工程が連続しているため、大量生産が可能であり、重量が大幅に軽減され、効率が向上するため、熱伝達効率を高めることができる。
たんぞうこうてい
鍛造技術はアルミニウムブロックを加熱した後、アルミニウムブロックを降伏点まで加熱し、高圧を利用して金型内に充填して形成したもので、フィンの高さは50 mm以上、厚さ1 mm以下に達することができ、同じ体積内で最大の放熱面積を得ることができ、しかも鍛造は容易に良好な寸法精度と表面仕上げ度を得ることができる。しかし、鍛造時、冷却塑性レオロジー時に首縮現象があるため、放熱フィンに厚さが薄く、高さが不均一な場合が発生しやすく、さらに放熱効率に影響を与え、金属の塑性が低く、変形時に亀裂が発生しやすく、変形抵抗が大きく、大トン数(500トン以上)の鍛造プレス機械が必要であり、設備と金型の高い費用のために製品コストが極めて高い。また、設備及び金型の費用が高いため、大量生産しない限りコストが高すぎる。
世界中で現在、冷間鍛造フィンを製造できるメーカーは多くなく、最も有名なのは日本のALPHAであり、台湾はTaisol、MALICO-太業科技である。冷間鍛造の利点は、アルミニウム押出よりも放熱面積の大きい放熱フィンを製造することができ、アルミニウム押出製造過程は延伸であるため、アルミニウム金属組織は水平方向に拡大し、冷間サテン方向は垂直に圧縮されるため、放熱については冷間鍛造が大きな利点を占め、欠点はコストが高く、製造可能な技術を持つメーカーも多くないことである。
形材放熱器の全体の製作過程は非常に細かく、各段階
前のページです
次ページです
関連ニュースです
電子放熱器は発熱体の熱の放出を加速する装置であり、放熱器の良否を測定するには2点がある:放熱と静音、電子放熱器の役割はこれらの熱を吸収し、それから筐体内または筐体外に発散し、コンピュータ部品の温度を正常に保つことである。
詳細を調べます私たちは、電子放熱器の耐久性は多種の要素に関連しており、電子放熱器の使用寿命を決定する主なものは、水質が基準を満たし、運行規範、選択が正しく、製品が合格していることを知っている。複数回の試験を経て、電子放熱器の水質に対する要求が他の放熱器を超えていることが分かった。
詳細を調べます形材放熱器は現在の社会で広く使用されており、ますます多くの人に愛用されている。では、どのような機能がこれほど多くのハートを得ることができるのでしょうか。次に復号しましょう!
詳細を調べます